Design Subteam Progress

Milestones
Timeline
Read about our progress milestones starting in September of 2024 and what we have planned for the future.

Outer Socket
Spring:
April - June2025
Strap Redesign & Concept Expansion
We redesigned the strap system, moving away from bulky ski-boot hardware and unreliable velcro. The new solution features pack straps anchored to embedded holders within the 3D-printed socket for better compression and usability. We also developed and tested a slotted socket concept, with varying infill densities. High-infill prototypes held up to ~160 lbs, validating the structural integrity of the design and informing future iterations.

Winter:
January - March 2025
Structural & Interface Improvements
To improve durability, we added fillets between the socket walls and base, preventing shear failures seen in previous versions. We also compared 2 mm and 4 mm wall thicknesses, finding the thinner, filleted model surprisingly robust. Meanwhile, we transitioned from a 4-hole adapter to a threaded pyramid adapter system, allowing for easier reuse and a more secure connection using a metal disc interface glued to the base.
![[Old] Three petal Design Without Velcro Straps - Onshape.png](https://static.wixstatic.com/media/6be05e_0009864c23c243aea119c8753a0110ce~mv2.png/v1/fill/w_151,h_196,al_c,q_85,usm_0.66_1.00_0.01,enc_avif,quality_auto/%5BOld%5D%20Three%20petal%20Design%20Without%20Velcro%20Straps%20-%20Onshape.png)
![[Old] Three petal Design With Velcro Straps - Onshape.png](https://static.wixstatic.com/media/6be05e_8f2399edfada4750bb4814d2463e17d5~mv2.png/v1/fill/w_151,h_218,al_c,q_85,usm_0.66_1.00_0.01,enc_avif,quality_auto/%5BOld%5D%20Three%20petal%20Design%20With%20Velcro%20Straps%20-%20Onshape.png)
Fall:
September - December 2024
Redesign & Early Prototyping
After identifying critical limitations in earlier socket designs—such as lack of flexibility and poor structural integrity—we began developing a new outer socket. Inspired by Patellar-Tendon-Bearing (PTB) models, we created a three-petal design for improved fit and support. Our first PLA prototype with 2 mm thick walls showed promising flexibility but ultimately failed due to weak wall-base joints, leading us to explore structural improvements.


Inner Socket
Fall-Spring:
September 2025- June 2026
Inner Socket Development
The inner socket evolved alongside changes to the outer socket design, with a focus on comfort, pressure distribution, and modularity.
​
In Fall '24, early development focused on two directions: a soft gel-like liner or a paneled foam system integrated with the outer socket. The team explored liner technologies, adjustable panel features, and suspension systems, researching how best to cushion and secure the limb within the evolving outer socket structure.
​
By Winter '25, the team moved forward with a multi-layered foam design using Poron foam for targeted pressure relief. Soft base foam was shaped to match pressure-sensitive areas of the transtibial stump, guided by load distribution research. A thin hard foam cap was added for a smooth, stable finish, and all edges were rounded for user comfort.
​
In Spring '25, the inner socket concept was updated to align with the ski-boot-inspired outer shell. A mesh sleeve system was introduced: a thin, contoured hard foam cup (inspired by leather cutting patterns) fits inside an athletic mesh sleeve, secured to the outer socket using industrial velcro. Additional ⅜-inch foam padding was added inside the sleeve to enhance cushioning and reduce pressure points.
​
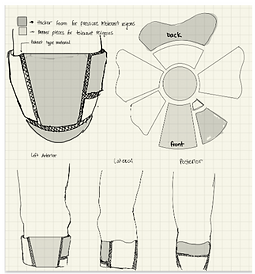